Publisher: Elsevier B.V.
URL: https://doi.org/10.1016/j.procir.2023.01.016 
8 July 2023
Abstract:
Future vehicles are connected, autonomous and shared platforms that render a multitude of services in our everyday lives. The vehicle’s driving function will ultimately converge to a commodity sourced by superstructure manufactures that develop service-oriented functionality. For the early stage vehicle concept design, this new functionality imposes a new complexity for superstructure engineers. Novel service offerings translate into new functional requirements and technical components that need to be optimally sized and positioned inside the vehicle package to increase the amount of service units that can be supplied to the customer. Today, vehicle concept design optimization only focuses on powertrain components.
In this paper, we introduce a novel two-step package design optimization for vehicle superstructures. First, functional requirements are derived from service units, the smallest unit of value to the vehicle-based service customer. We then develop component weight and size regression models from
data retrieved from online warehouses. Components and their installation constrains are represented by scalable containers. A combined packing heuristic and parameter optimization arranges the containers within the vehicle’s available installation space and created layout alternatives. We apply this procedure to a real case study based on the aCar, a light electric utility vehicle for rural sub-Saharan Africa. This is a first step to enable superstructure manufactures to design and optimize vehicle concept designs based on service capacity.
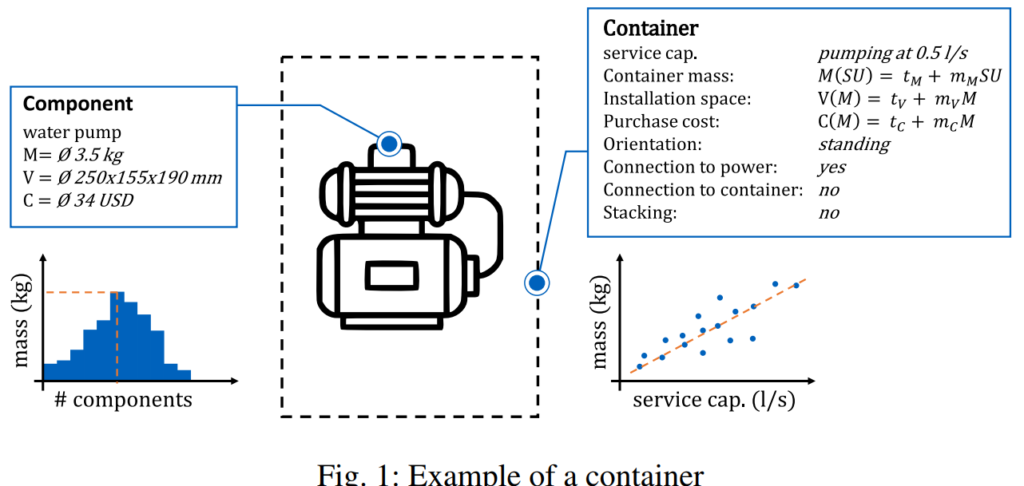
Screenshots from the methodology and the study case information:
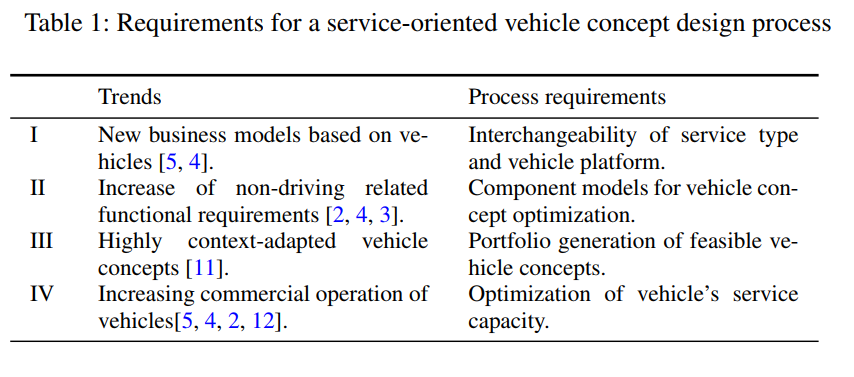


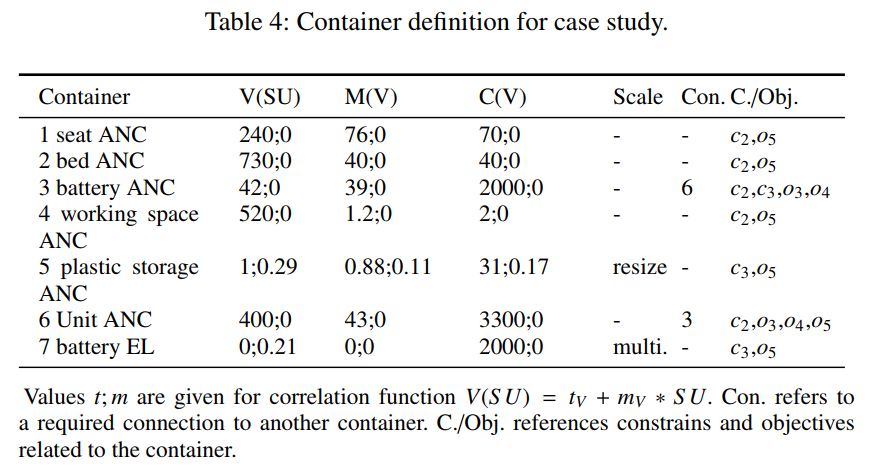

Limitations and discussion:
For our case study, we have shown that all four requirements (table 1) can be addressed, but there are several limitations that should be addressed in further research on package design optimization for vehicle-based service. At the moment, we are only able to consider cuboid containers and installation spaces. Cagan et al. [22] have shown that other shapes can be considered with increasing model complexity.
Further, duplicates of multipliable containers are always placed consecutively, therefore preventing any other possible layouts. Most importantly, the optimization is limited by the packing heuristic’s potential to create varieties of feasible layouts. With the optimizer being able to vary the fixed point to which the distance of containers is maximized, a greater set of feasible layouts could be generated. Nevertheless, we consider our contribution to the field of vehicle package design optimization twofold. First, the idea of vehicle service capacity as a design objective that can also be adopted by exiting concept design tools ([16, 14, 15]. Second, the introduction of a two-step design optimization that can be applied across services and vehicle platforms during an early design stage. This service-dominant logic in vehicle design is unprecedented at the moment and in the light of the automotive megatrends, we expect to see more research focusing on the vehicle as a service platform.
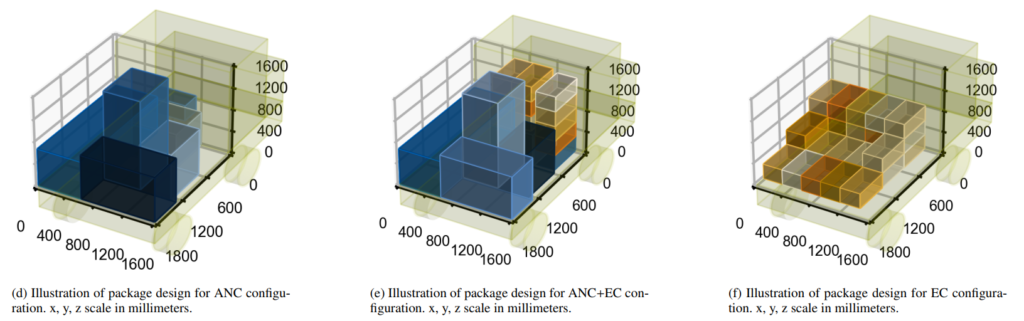

References:
[14] Kai Kuchenbuch, Thomas Vietor, and Jurgen Stieg. Optimierungsalgorith- ¨ men fur den Entwurf von Elektrofahrzeugen. ¨ ATZ – Automobiltechnische Zeitschrift 2011 113:7, 113(7):548–551, 7 2011. doi: https://doi.org/10. 1365/S35148-011-0128-7.
[15] Stephan Matz. Nutzerorientierte Fahrzeugkonzeptoptimierung in einermultimodalen Verkehrsumgebung. Dissertation, 2015.
[16] Lorenzo Nicoletti, Sebastian Mayer, Matthias Bronner, Ferdinand Schock- ¨ enhoff, and Markus Lienkamp. Design Parameters for the Early Development Phase of Battery Electric Vehicles. World Electric Vehicle Journal 2020, Vol. 11, Page 47, 11(3):47, 6 2020. doi: https://doi.org/10.3390/ WEVJ11030047 .
[22] J. Cagan, K. Shimada, and S. Yin. A survey of computational approaches tothree-dimensional layout problems. Computer-Aided Design, 34(8):597– 611, 7 2002. doi: https://doi.org/10.1016/S0010-4485(01)00109-9 .